Φ4.27m*6.5m Ball Mill Liners: Enhancing Efficiency and Durability in Industrial Grinding
Ball mills are essential equipment in the mining and mineral processing industries, playing a crucial role in grinding operations. The performance and efficiency of a ball mill are significantly influenced by the quality of its liners. This article focuses on the Φ4.27m*6.5m ball mill liners, examining their features, benefits, and importance in the industrial sector.
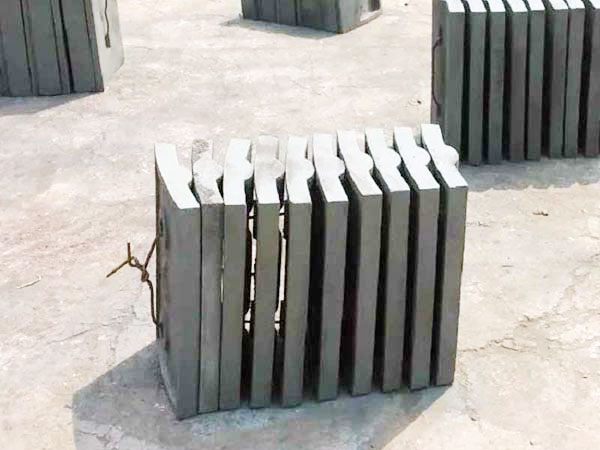
Importance of Ball Mill Liners
Ball mill liners serve multiple purposes: they protect the mill shell from wear and tear, enhance grinding efficiency, and extend the lifespan of the equipment. High-quality liners ensure the smooth operation of the mill, reducing downtime and maintenance costs. For the Φ4.27m*6.5m ball mill, selecting the right liners is paramount to achieving optimal performance.
Features of Φ4.27m*6.5m Ball Mill Liners
1. Material Composition: The liners for the Φ4.27m*6.5m ball mill are typically made from high-manganese steel, chrome-molybdenum alloy, or rubber. High-manganese steel liners are known for their toughness and resistance to impact wear, making them ideal for heavy-duty applications. Chrome-molybdenum alloy liners offer excellent wear resistance and corrosion protection, while rubber liners provide noise reduction and a longer lifespan.
2. Design and Structure: The design of the liners is critical to their performance. The Φ4.27m*6.5m ball mill liners feature a corrugated structure that enhances the grinding action by lifting the charge higher and increasing the impact energy. This design improves the efficiency of the grinding process, resulting in finer particle size distribution.
3. Customization: These liners can be customized to meet specific operational requirements. Factors such as mill speed, ore characteristics, and grinding media size are considered during the design process to ensure optimal performance. Customization allows for better adaptation to varying grinding conditions, enhancing overall efficiency.
4. Durability: The durability of the Φ4.27m*6.5m ball mill liners is a key feature. High-quality materials and advanced manufacturing techniques ensure that these liners withstand the harsh conditions of industrial grinding. Their long service life reduces the frequency of replacements, minimizing operational disruptions.

Benefits of High-Quality Ball Mill Liners
1. Enhanced Grinding Efficiency: High-quality liners improve the grinding efficiency of the ball mill by optimizing the motion of the grinding media. This results in more effective particle size reduction, increasing the throughput and productivity of the mill.
2. Reduced Maintenance Costs: Durable liners reduce the need for frequent replacements and repairs, leading to lower maintenance costs. This is particularly important in large-scale operations where downtime can be costly.
3. Improved Safety: Properly designed and installed liners enhance the safety of the grinding operation. They protect the mill shell from damage, reducing the risk of structural failures that could lead to accidents.
4. Noise Reduction: Rubber liners, in particular, offer significant noise reduction benefits. This is crucial in maintaining a safer and more comfortable working environment in industrial settings.
Applications of Φ4.27m*6.5m Ball Mill Liners
1. Mining Industry: In the mining industry, ball mills are used for grinding ores to extract valuable minerals. The Φ4.27m*6.5m ball mill liners are specifically designed to handle the abrasive nature of the ores, ensuring efficient grinding and prolonged equipment life.
2. Cement Industry: Ball mills are also widely used in the cement industry for grinding clinker and other raw materials. The robust design of the Φ4.27m*6.5m ball mill liners ensures that they can withstand the harsh conditions and high temperatures of the cement grinding process.
3. Power Plants: In power plants, ball mills are used for pulverizing coal to prepare it for combustion in the boiler. High-quality liners are essential to ensure the efficient grinding of coal and prevent the wear and tear of the mill.
4. Chemical Industry: Ball mills in the chemical industry are used for grinding various materials to achieve the desired chemical reactions. The durability and customization options of the Φ4.27m*6.5m ball mill liners make them suitable for a wide range of chemical grinding applications.
Choosing the Right Liners for Φ4.27m*6.5m Ball Mills
Selecting the right liners involves considering several factors:
1. Material Properties: The choice of liner material depends on the type of ore or material being ground, as well as the specific grinding conditions. High-manganese steel is suitable for impact resistance, while chrome-molybdenum alloy offers better wear resistance.
2. Mill Operating Conditions: Factors such as mill speed, feed size, and grinding media type influence the design and material selection for the liners. Customization based on these conditions ensures optimal performance.
3. Cost-Effectiveness: While high-quality liners may have a higher initial cost, their long-term benefits in terms of durability and reduced maintenance costs make them a cost-effective choice.
4. Manufacturer Reputation: Choosing liners from reputable manufacturers ensures that they meet the required quality standards and provide reliable performance. Reputable manufacturers also offer technical support and customization options.
Conclusion
The Φ4.27m*6.5m ball mill liners are a critical component in industrial grinding operations, providing protection to the mill shell, enhancing grinding efficiency, and extending the equipment’s lifespan. Their features, including material composition, design, customization options, and durability, make them suitable for various applications in the mining, cement, power, and chemical industries. By choosing high-quality liners, operators can achieve improved efficiency, reduced maintenance costs, and enhanced safety in their grinding operations.