Ball Mill Manufacturer
A ball mill is equipment designed for grinding hard materials such as marble, crushed stone, chalk, slag or expanded clay. Mills are also used to produce suspensions, emulsions and slaking of lime. The grinding process occurs using solid spherical bodies of varying densities and sizes. Balls are made of plastic, ceramics and various high-strength alloys.
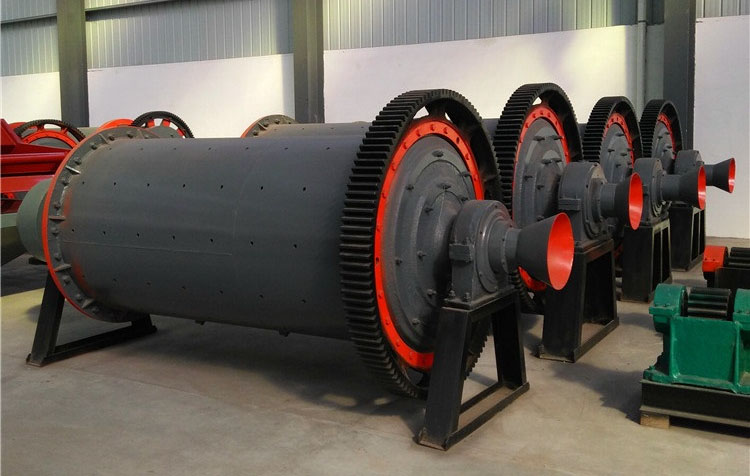
In industry, drum-type ball mills are most often used. This is a cylindrical container that rotates in a horizontal plane. Steel balls and grinding material are loaded into the container. In addition to steel balls, bodies of various shapes can be used – cylinders, prisms.
Construction
The main design element of a ball mill is a rotating cylindrical container or drum, which is partially filled with solid spherical bodies. The drum rotates using an electric motor. The balls are made of steel, cast iron, ceramic or plastic, depending on the material being crushed. The drum is closed with loading and unloading covers. The inner walls of the container are lined with fire-resistant, chemical-resistant and wear-resistant plates (linings), which include rubber or steel. The plates prevent the drum from the impact and friction of the balls. Linings, depending on the size of the crushed material, have ribs of different heights. The height, location and shape of the fins determine the performance of the mill.
Principle of operation
The ball mill rotates continuously. During the rotation process, the crushed material is loaded into the drum through the central hole in the lid. Next, the material is crushed using spherical bodies.
The grinding of the material occurs at the moment of impact of the falling grinding balls and the abrasion of its particles between the balls. During grinding, the material is subjected to impact and abrasive forces.
Depending on the properties and characteristics of the loaded material, the grinding time ranges from several minutes to several tens of minutes.
The crushed material is then discharged through the central opening of the discharge cover.
Depending on the rotation speed of the mill, one of the following operating modes is distinguished:
- ascade – mode of motion of spherical bodies with rolling and without flight;
- mixed – mode of movement of grinding balls with partial rolling and flight;
- waterfall – mode of grinding balls with their predominant flight
The rotation speed affects the grinding quality of the material. At low speed, grinding is carried out by grinding the material being ground with grinding bodies sliding and rolling along the surface of the drum. At medium speeds, the impact on the source material is exerted by spherical bodies, which rise to a certain height during rotation. Crushing of material at high speed occurs due to the influence of centrifugal force.
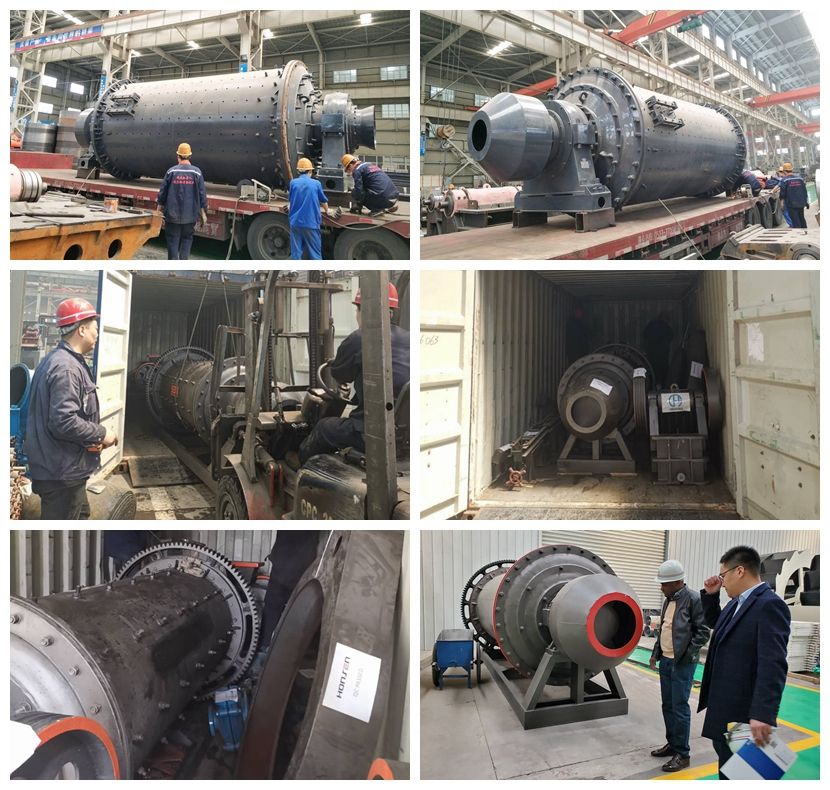
Classification of ball mills
Depending on the characteristics, design and scope of use, several types of ball mills are distinguished.
By area of use they distinguish:
- Industrial are units that have high productivity and operate in continuous mode.
- Laboratory – they are small in size and process a small amount of material. They operate in periodic mode.
Depending on the design, ball mills come with one or two drums. In this case, the drums can be cylindrical or have a cylindrical-conical shape.
According to the method of processing the material, ball mills are distinguished:
- Wet grinding – the device is used for processing ores and mining chemical raw materials, in the production of paints and varnishes, glass and ceramics.
- Dry grinding – equipment is used for the production of chemical compounds and building materials.
Depending on the operating mode, ball mills can be either continuous or intermittent.
Equipment is also distinguished according to the method of unloading crushed material. For central unloading, the equipment is called lattice or drain. Such equipment is characterized by high productivity, while unloading occurs forcibly. There is also a group of drain ball mills, the discharge of which is carried out through the trunnion threshold.
Most often, ball mills with unloading through a grate are used in the production cycle. Such equipment has a number of advantages:
- the final product is uniform in fractions;
- low sludge content, which is achieved due to the fact that the unloading hole is located below the loading level;
- increased productivity compared to drain type equipment.
- adjustment of the degree of grinding and the ability to load material in fractions up to 30-35 mm;
- Thanks to the ability to increase the opening in the diaphragm, productivity can be increased.
Ball mill capabilities
Ball mills operate in both open and closed technological cycles. They make it possible to obtain a finished material that is homogeneous in fineness, which is crushed using spherical bodies.
Equipment performance depends on the properties and characteristics of the loaded material. First of all, strength, fraction size when loading, humidity, grinding fineness, drum filling and uniformity of feeding are taken into account.
Specifications:
- diameter of balls, mm – from 30;
- fraction size at the inlet, mm – up to 50;
- output grinding fineness, microns – up to 2;
- drum diameter, mm – from 900;
- drum length, mm – from 1500;
- drum volume, cubic meters m. – from 0.9;
- electric motor power, kW – from 18;
- operating voltage, V – 380;
- productivity, t/h – from 2;
- weight, kg – 5000.
Applications of ball mills
Designed for dry and wet grinding of various ore and non-metallic minerals, building materials of varying hardness.
- grinding of raw materials and clinker in cement production
- crushing marble in the production of microcalcite
- grinding of non-metallic minerals in the production of gypsum, mineral powder
- grinding of various materials
- coal grinding at thermal power plants with pulverized coal boilers
How to choose a ball mill?
When choosing a ball mill, it is necessary to proceed from the size of the fractions of the source material, the characteristics of the equipment and the properties of the raw material itself. Some grinding materials have a dense structure, high hardness and small crystals. In this regard, such material is difficult to process and requires a longer time for grinding. In addition, such raw materials require high-performance equipment, and in this case, solid spherical bodies are used for grinding.
Ball mills have high adaptability to various materials, and are used to grind slag, various ores or aluminum ash.
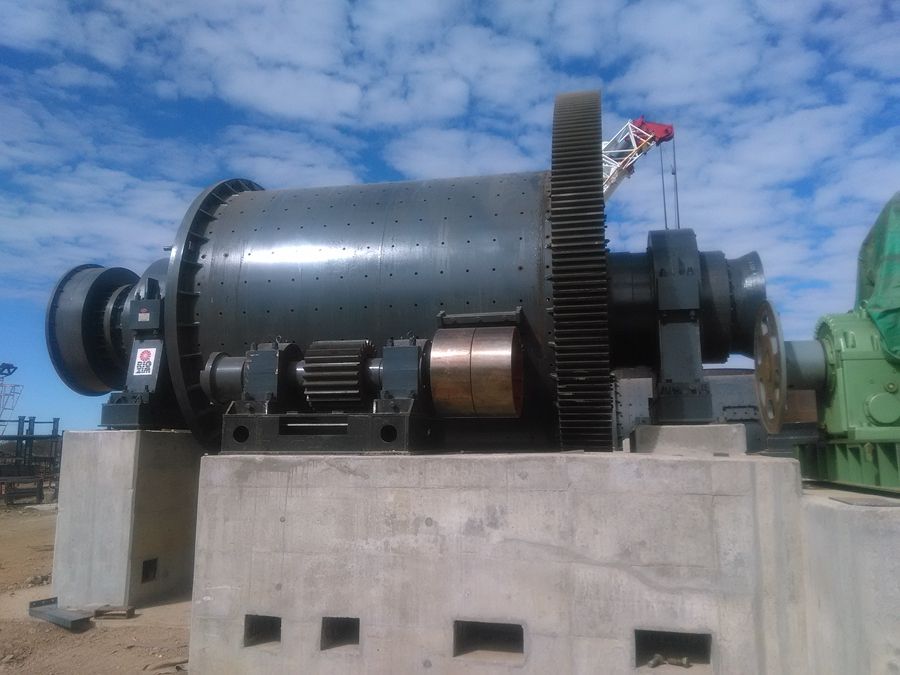
Steel balls are often used for grinding in ball mills. During the grinding process, the steel ball has a targeted effect on the grinding products. As a result, the grinding product is highly fine and the particle size is very small. Due to these subtleties of the process, a ball mill is not suitable for enterprises involved in ore beneficiation.
The feed particle size in a ball mill ranges from 5 to 25 mm.
Review of ball mill models
A series of machines are used for crushing and grinding. Quickly transforms large solid materials into fine powder. Used for single-stage fine grinding and as a second stage in a double grinding circuit. They are used in processing factories, for the production of cement, silicate products, building materials, paints, chemical fertilizers, ferrous and non-ferrous metals, glass and ceramics.
The grinding materials inside the operating chamber are steel balls made of stainless steel or ceramics. The diameter of the balls depends on the application and ranges from one to several centimeters.
Characteristics:
- Rotation speed, rpm – 23.7;
- Ball load mass, t – 24;
- Final fractions, mm – 0.074-0.4;
- Weight, t – 42;
- Power, kW – 245;
- Productivity – 8-43;
- The maximum size of loaded material is 25 mm.
Ball mill Ф2100×3000
The equipment is designed for grinding raw materials after the crushing process. They are used in the production of building materials such as gypsum, sand-lime brick, and dry mixes.
Characteristics:
- Rotation speed, rpm – 23.7;
- Ball load mass, t – 15;
- Final fractions, mm – 0.074-0.4;
- Weight, t – 34;
- Power, kW – 210;
- Productivity – 5-36;
- The maximum size of loaded material is 25 mm.
Ball mill Ф1830×7000
It is used in ore dressing, in the production of building materials and in the chemical industry. The device is an effective tool for medium and fine grinding of fireclay, coal, non-metallic minerals and other non-plastic materials. Used for the production of grinding cement, silicate products, building materials, refractory materials, fertilizers, non-ferrous metals, glass and ceramics. Grinding method: dry.
Advantages:
- maintainability;
- reliability;
- high performance.
The design feature is that the chamber has stepped and corrugated plates. The grinding chamber is filled with steel balls of different sizes. The crushed material falls out through the grate, after which the grinding process is completed.
Characteristics:
- Rotation speed, rpm – 24.1;
- Ball load mass, t – 23;
- Final fractions, mm – 0.074-0.4;
- Weight, t – 36;
- Power, kW – 245;
- Productivity – 7.5-17;
- Maximum size of loaded material, mm – 25.
Ball mill Ф1830×6400
It is used for dry and wet grinding of various ore and non-metallic minerals, medium-hard building materials – clinker, cement raw materials, mining raw materials, iron ore concentrate. Grinding occurs to the size of sand and dust fractions, turning the source material into mineral powder.
Characteristics:
- Rotation speed, rpm – 24.1;
- Ball load mass, t – 21;
- Final fractions, mm – 0.074-0.4
- Weight, t – 34;
- Power, kW – 210;
- Productivity – 6.5-15;
- Maximum size of loaded material, mm – 25.
Ball mill Ф1830×4500
It is used in the production of various types of cement, silicate material, refractory materials, as well as in the construction and chemical industries. There are dry and wet grinding mills.
Features:
Rotation speed, rpm – 25.4;
Ball load mass, t – 15;
Final fractions, mm – 0.074-0.4;
Weight, t – 32;
Power, kW – 155;
Productivity – 4.5-12;
Maximum size of loaded material, mm – 25.